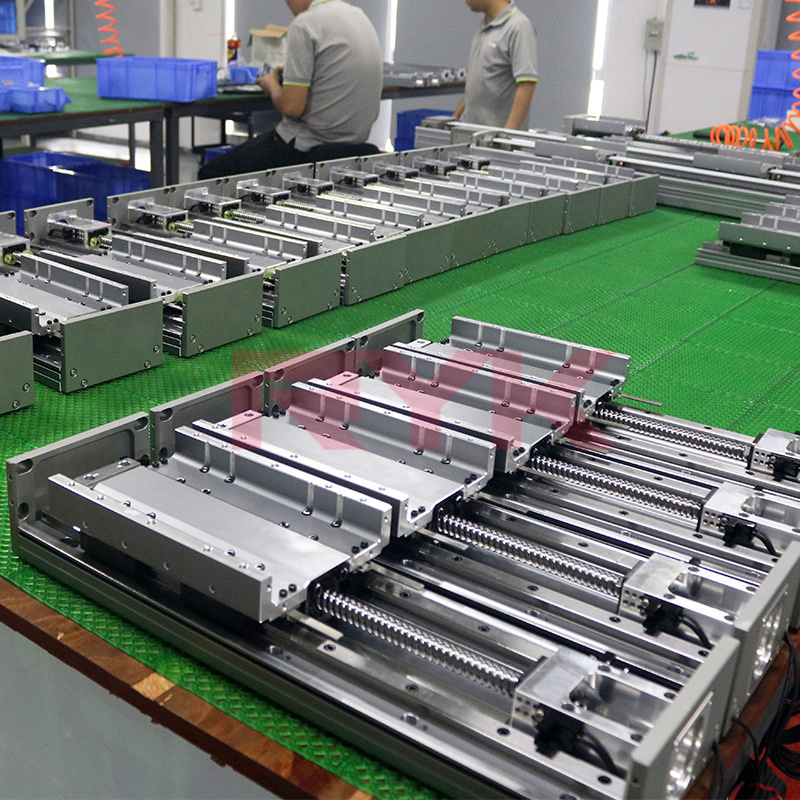
Selecting the right linear motion system for your project can be challenging, especially when distinguishing between stroke and lead. At RYK Motion Technology, we simplify these crucial parameters to help you choose the ideal linear module for your needs. This guide will explain the key differences and their impact on your system’s performance.
Understanding Stroke in Linear Modules
The stroke (or travel distance) refers to the maximum movement range of the carriage along the linear guide in a linear module. Specifically, the effective stroke is the distance between the carriage’s starting point and its furthest reachable position during operation.
Key Characteristics of Stroke:
-
Determines the working range of your automation system.
-
Directly impacts machine design, installation space, and overall system efficiency.
-
Standard stroke ranges typically vary from 100mm to 3000mm in modular linear guide systems.
For more technical details, refer to our product specifications or consult the ISO 3408-1 ball screw standard.
Defining Lead in Ball Screw Modules
Lead refers to the distance the carriage moves with one complete revolution of the ball screw. Common lead sizes include 5mm, 10mm, and 20mm, which affect the performance characteristics of the linear module.
Performance Implications of Lead Size:
Lead Size | Speed Potential | Load Capacity | Typical Applications |
---|---|---|---|
5mm | Lower | Higher | Precision positioning |
10mm | Moderate | Balanced | General automation |
20mm | Higher | Lower | High-speed transport |
For more in-depth technical information on lead sizes and ball screw mechanics, refer to our engineering whitepaper.
Critical Differences Between Stroke and Lead
-
Fundamental Nature:
-
Stroke: Refers to the physical movement limit or maximum travel distance of the carriage.
-
Lead: Represents the mechanical transmission ratio of the ball screw, dictating how far the carriage moves with each revolution of the screw.
-
-
Selection Priority:
-
Stroke: Primarily determines the module length and overall travel distance.
-
Lead: Influences the speed and force characteristics of the system.
-
-
Design Impact:
-
A larger stroke requires a more robust guiding system (refer to THK Linear Guide Technical Guide).
-
A smaller lead enhances positioning resolution, ensuring more precise control over movement.
-
How to Choose the Right Combination of Stroke and Lead?
-
Step 1: Calculate the required stroke based on your application needs.
-
Step 2: Select the appropriate lead based on:
-
Speed requirements (V = lead × RPM).
-
Available motor torque and power.
-
Desired positioning accuracy.
-
Pro Tip: Use RYK Motion’s online configurator tool to visualize different stroke/lead combinations and identify the best match for your application.
Why This Matters for Your Application
Different industries and use cases require different combinations of stroke and lead. For example:
-
Laser cutting: Often requires a long stroke with a medium lead to balance precision and speed.
-
Packaging lines: Typically use short strokes with a high lead for rapid movement and efficiency.
-
Medical devices: Demand compact strokes and small leads for micron-level precision and accuracy.
For complex applications, reach out to our engineers through RYK Motion’s technical support portal.
Conclusion
-
Stroke = Maximum travel distance (determines the module size and design).
-
Lead = Distance moved per screw revolution (affects speed, force, and precision).
If you’re still unsure which stroke and lead combination suits your application, download our Linear Module Selection Handbook or contact us directly at WhatsApp/Wechat +86-13592795134 for personalized assistance.