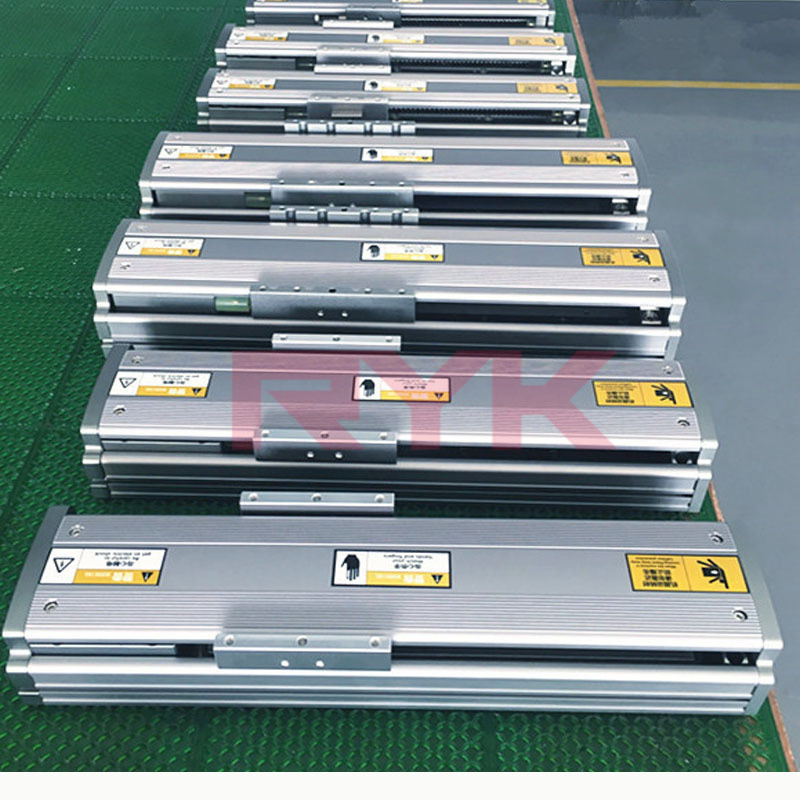
Linear modules and linear motors are both key components in automation systems, commonly used in precision machinery, robotics, and industrial automation. Despite their similar appearances, featuring aluminum housings with cover plates, they differ significantly in terms of working principles, performance, and applications. Understanding these differences is essential for selecting the optimal solution based on factors like speed, precision, and cost.
1. Linear Motion Principle: Core Mechanism
-
Linear Motor Stage: Converts electrical energy directly into mechanical motion (via Lorentz force), eliminating intermediate mechanisms. This “direct drive” design reduces energy loss. (Reference: MIT Linear Motor Research)
-
Linear Module: Relies on rotary-to-linear conversion through ball screws or timing belts, introducing mechanical complexity.
Keywords: direct drive linear motor, rotary-to-linear conversion, ball screw mechanism
2. Accuracy Comparison
-
Linear Motor Stage: Achieves ±0.001mm precision due to no backlash or mechanical hysteresis. Ideal for semiconductor and laser cutting applications.
-
Linear Module: Typical accuracy ranges from ±0.005mm to ±0.04mm (ball screw type). Synchronous belt modules offer lower precision.
Pro Tip: For ultra-high precision, linear motors outperform modules but cost more.
3. Speed and Acceleration
Parameter | Linear Motor | Linear Module (Ball Screw) |
---|---|---|
Max Speed | 300 m/min | 120 m/min |
Acceleration | Up to 10G | ~1.5G |
Dynamic Response | 1:10,000 speed range | Limited by inertia |
Why It Matters: Linear motors excel in high-speed pick-and-place or CNC machines. Modules suit slower, high-force tasks.
Keywords: high-speed linear actuator, servo motor acceleration
4. Noise Levels
Linear motors operate near-silently (no mechanical contact), while modules generate noise from rolling elements (ball screws) or belt teeth. For quiet environments (e.g., medical labs), linear motors are preferable.
External Link: Noise Reduction in Automation (ISO Standards)
5. Cost Considerations
Linear motors cost 3–5× more than modules due to advanced materials and precision. However, their longevity and reduced maintenance can lower TCO (total cost of ownership).
Budget Tip: Sync belt modules are the most economical for long travels (>3m).
How to Choose? Decision Guide
Requirement | Recommended Solution |
---|---|
High speed, long stroke | Linear Motor |
High force, short stroke | Ball Screw Linear Module |
Medium force, long stroke | Timing Belt Linear Module |
Explore RYK Motion Solutions: